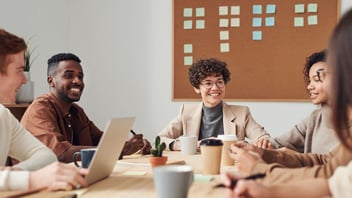
Are you 'lean' enough?

In the current economic climate everyone is talking about the importance of being 'lean'. But what does it mean to be lean and are your efficiency measurements actually hiding opportunities for improvement?
Steve Roger, managing director of Lauras International Pty Ltd and Jeremy Praud, partner of Lauras International Europe LLP provide a few tips to help companies measure their losses correctly as the key to becoming lean...
In the landmark book, The Machine That Changed the World: The Story of Lean Production, authors Womack, Jones and Roos chronicle the automobile industry's evolution from mass production to lean production. The term 'lean' was coined by the authors to describe Toyota's successful production system. Indeed Toyota's efficiency was remarkable - in the 1980s it took 17 hours for a Toyota car to be built and ready to ship, whereas a Mercedes spent that amount of time in the rework area alone. The Toyota Production System (TPS) transformed this small post-war Japanese car company into a world leading car manufacturer, and has become a model for efficient production worldwide.
The core aim of being lean is to eliminate 'non-value adding' activities (i.e. those that customers wouldn't want to pay for) in order to compress production time and create competitive advantage by optimising resources (i.e. people, space and capital).
Toyota defined seven types of waste (muda) to describe 'non-value adding' activities:
- Overproduction
- Defects
- Inventory (more than minimal)
- Transport (further than required)
- Waiting
- Motion
- Processing (unnecessary).
They applied key principles to reduce these wastes, including 'Right First Time Quality' (jidoka) - or the quest for zero defects and 'Just In Time' (JIT) production - or reducing the costs associated with inventory.
Each key principle has associated tactics. 'Right First Time Quality', for example, involves mistake proofing (poka yoke), 'One Piece Flow' (i.e. having a batch size of one to detect defects immediately) and 'Stop The Line' (i.e. authorising employees to stop the line for a defect - the expense involved in stopping the line helps to fix the problem).
JIT reduces inventory through 'One Piece Flow' and 'Pull' production - or making only what the customer wants, and stops expensive overproduction.
JIT principles include:
- Tightly controlling small quantities of strategically placed inventory (kanban);
- 'Single Minute Exchange of Dies' (SMED) - reducing the time to change products means the stock can be minimised; and
- 'Production Smoothing' - making sure your production line is flexible enough to produce a diversity of products without compromising efficiency.
- Over the past two decades all of these principles and tactics have been successfully used in many manufacturing and non-manufacturing businesses worldwide. So why do many businesses not achieve the benefits expected?
- Probably the main reason businesses fail to become lean is because they don't know how to measure their losses correctly.
Here are four common mistakes that businesses make when measuring efficiency:
- Measuring activity, not productivity - An administrator notices a mistake whilst processing forms - she gets a fax confirmation and corrects the transaction. She ticks the boxes for 'missing data' and 'confirmation fax', which gives an extra allowance of 60 minutes. Although the transaction took 90 minutes instead of the normal 30 minutes, her efficiency holds up because of the extra activity.
- Ignoring the elephant in the room - Many companies mistakenly exclude losses that are no longer seen as problems. Remember, it is better to include losses than overlook them completely. Ignoring a problem won't make it go away.
- Using the wrong bottleneck speed - A common pitfall, and one that is hard to spot, is that many organisations allow say 20 minutes for a phone call, when the call could have been be made in 10 minutes. I could spend all morning making calls, stop at lunchtime, and still report 100% efficiency, when in fact my efficiency is under par.
- Confusing the target with 100% - Some organisations seem to feel bad about admitting to a low efficiency, so they have standards with hidden allowances. Unfortunately, making allowances and 'hiding' losses doesn't help us improve.
So what to do about it? Here are a few things you can do right away to become more lean:
- Ask what is included in your efficiency measure. Listen carefully. The only correct answer is 'everything'.
- Ask a few of your senior team "What are the top three business losses?" If they come up with different answers, it's time to ask some tough questions.
- Actually watch a production line for 10 minutes. Check the output, and ask the operator what the maximum output could have been. If there is a difference, find out where it is recorded.
- If there are large variations in employees' workloads, but the job always gets done, ask yourself how. Also, find out what activities your employees undertake at the end of their shifts.
Ultimately, measures do drive behaviours, so make sure you're really measuring your biggest wastes - this is the first step to making your company lean.
Steve Roger is managing director of Lauras International Pty Ltd and Jeremy Praud is partner of Lauras International Europe. Lauras International partners with businesses to drive rapid and sustained bottom line improvement. Their core expertise is in training and implementing change. Please send any comments or questions you have in relation to this article to: stephen.roger@laurasinternational.com
Related
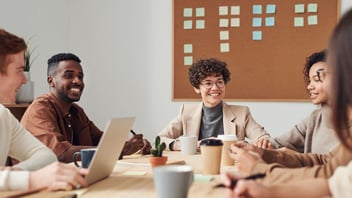
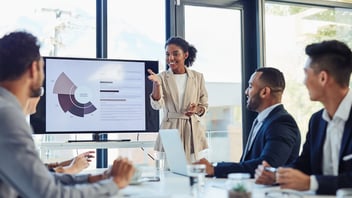
How learning and development drives talent retention and growth
In the ongoing quest to attract and retain top talent, organisations are discovering that offering...
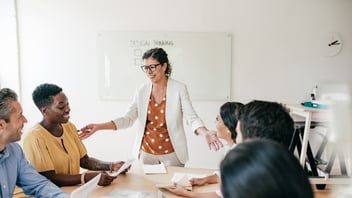
6 winning leadership traits you won’t see on a resume
Leaders once ascended to leadership positions in the C-Suite based on their expertise and as a...