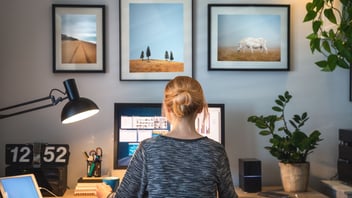
Does Warehouse Automation Take Over?
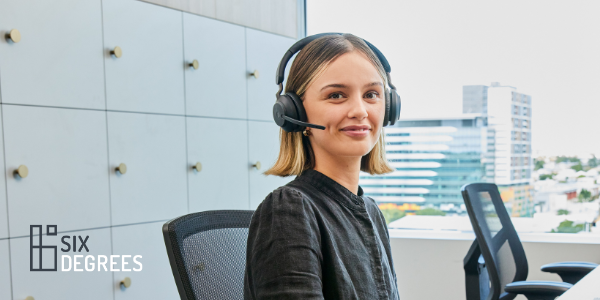
Warehouse automation is an increasingly talked about topic amongst Supply Chain Managers. In this article, Carolyn Schroten, National Logistics Solutions Manager at Coca-Cola Amatil, discusses the value of warehouse automation and details how this has improved efficiency at both their Northmead and Eastern Creek sites.
What are the key drivers to turn to automation?
There are various reasons which could drive the research into and subsequent implementation of warehouse automation. Some key reasons include:
- labour availability due to a low (operational expensed) labour rate strategy (ie. high turnover)
- aiming to eliminate physical handling (e.g. heavy lifting)
- OH&S reasons
- warehouse space constraints requiring a denser operating environment
- aiming to improve the efficiency of a single process.
Irrespective of the reason, automation should be part of long term warehouse strategies and may or may not have immediate tangible (short-term) savings.
When is it appropriate to automate processes?
As there is a lot of complexity involved in automation it isn't necessarily always the right solution to automate. Some things to consider are:
- Don't try to automate everything at once. Start with the simple and stable (constant) processes first.
- Break the processes down into distinct areas; can you achieve a first cut result by tackling only part of the larger problem?
- Understand the full end-to-end requirements - don't automate a process which will create a bottleneck in itself, the typical Theory of Constraints principle (John Goldrath). The processes feeding into or extracting from the automated process may create more of a bottleneck than first expected.
A classic example in warehousing is automating the internal warehouse process without consideration of the despatch process and subsequent traffic management at the docks. Ask yourself, 'has automation made the operation so efficient that the staging and dock areas are now overloaded with goods?'.
What have we done at CCA?
At CCA, Project Jupiter included the full automation of the full pallet storage warehouse at Northmead and semi-automation for the case picking warehouse at Eastern Creek. We automated the Northmead site for two key reasons:
- eliminating any handling of full pallets from production to order fulfilment
- increasing the density of storage on site
The Eastern Creek case pick facility services our smaller order sized customers and is therefore more reactive to order profile (quantity and range) changes of mixed pallets. Here we looked at the processes where it made sense e.g. the replenishment of stock from the Northmead production facility through automated skate docks. This eliminates all forklift handling (for loading and unloading) at both sites from production up to the point of putaway into the pickface at Eastern Creek.
We are continuously reviewing our processes and assessing when and how it makes sense to automate.
What does that mean with regards to the skills and capability in a company?
Implementing automation has a greater impact on the skill base of a company than most companies take into consideration. Understanding and operating automation will change the required skill set from a manual task driven environment (re-active) to a process focused and problem solving (analytical and pro-active) employee base.
It's important to ask yourself:
- is your HR department prepared for this change?
- can your incumbent workforce make that transition?
- where will you subsequently source new employees from in future?
As we have seen at CCA, automation certainly provides major benefits to an organisation, provided the process and people side is well planned and well transitioned.
Related
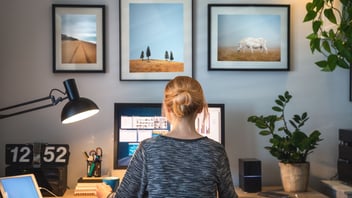
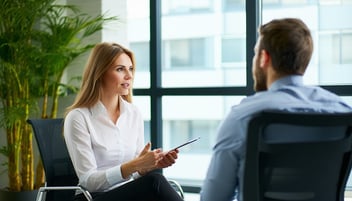
Overcoming imposter syndrome in interviews
Why do candidate struggle to “sell themselves” during an interview? What is the point of an...
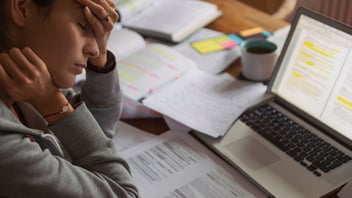
Understanding burnout – why it matters and what to do about it
Most of us understand the importance of taking time off work when we’re physically unwell or...